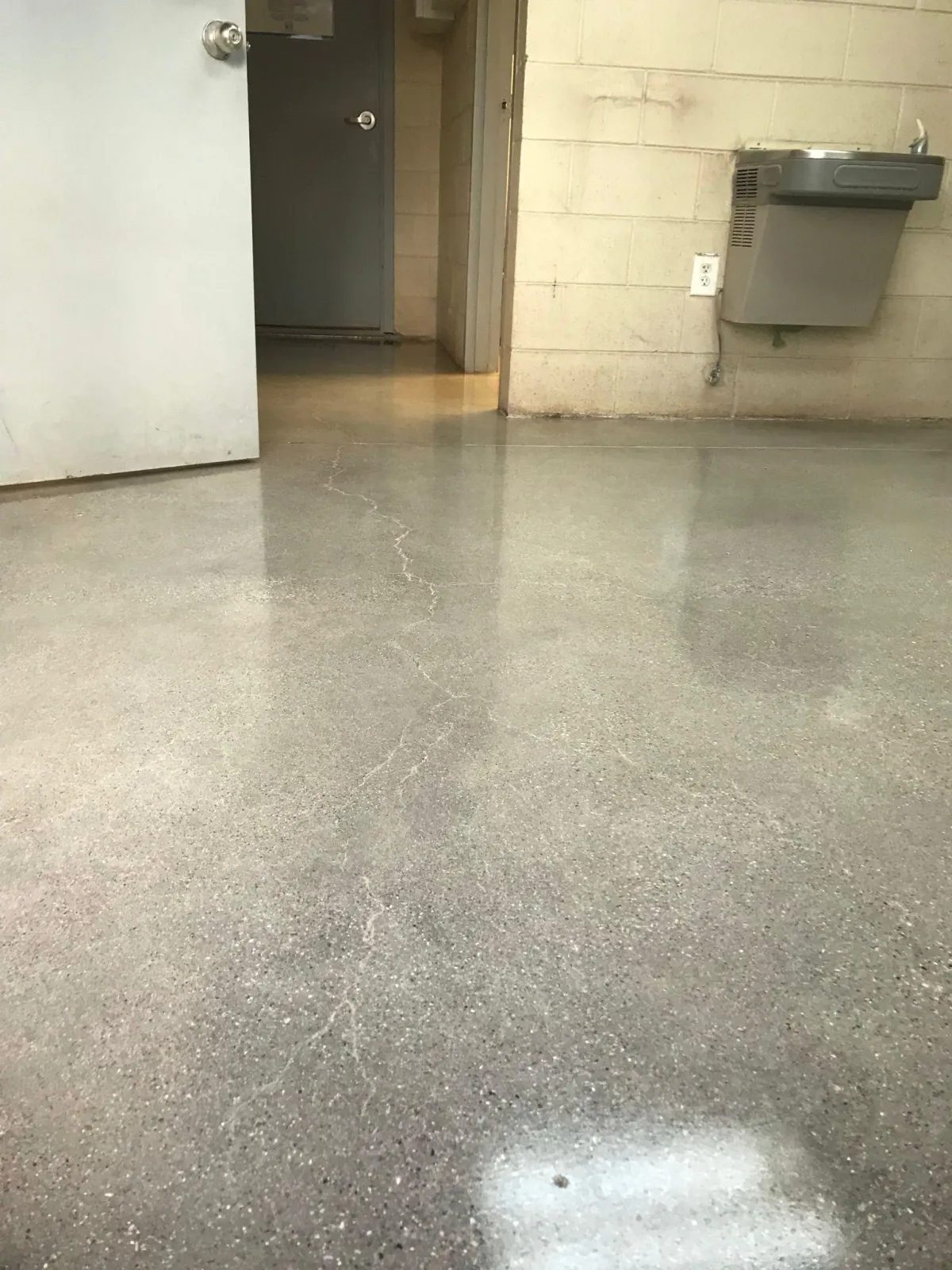
Architects & Designers Guide: How to Expertly Specify Polished Concrete Floors for Commercial Projects
Polished concrete has rapidly become one of the most sought-after flooring choices for commercial architecture—and with good reason. Offering exceptional durability, modern aesthetics, sustainability, and ease of maintenance, polished concrete aligns perfectly with the priorities of architects and designers working on contemporary commercial projects. But to truly achieve the promise of polished concrete, careful and detailed specification is crucial. Oversights in design or material selection can lead to disappointing results, costly repairs, or project delays. At Ayala’s Concrete Designs in St. George, UT, we've seen firsthand the impact a well-specified polished concrete floor can make. In this guide, we’ll share practical insights and industry know-how, helping you specify polished concrete confidently, avoid common pitfalls, and deliver stunning floors that surpass client expectations.
Table of Contents
Understanding the Basics: What Exactly is Polished Concrete?
Key Considerations for Concrete Mix Design
Choosing the Right Level of Aggregate Exposure and Finish
Why Moisture Control is Critical for Polished Concrete Floors
Accounting for Joints, Cracks, and Imperfections
Specifying Slip Resistance and Ensuring ADA Compliance
Properly Specifying Polished Concrete Maintenance Plans
Working with a Trusted Polished Concrete Contractor
Bringing Your Polished Concrete Vision to Life
1. Understanding the Basics: What Exactly is Polished Concrete?
Before diving into the detailed specifications, it’s crucial to clearly understand what polished concrete actually is—and just as importantly, what it isn’t. Polished concrete flooring is not simply concrete with a shiny sealer or coating applied on top. Instead, it's created through a precise, multi-step mechanical process that involves progressively grinding, honing, and polishing the concrete slab. This process refines the surface, revealing its inherent beauty and increasing its hardness, density, and resistance to wear.
In commercial applications—such as retail spaces, hotels, office buildings, restaurants, and even industrial facilities—polished concrete offers a unique blend of style, performance, and sustainability. Architects and designers appreciate polished concrete not only for its minimalist, contemporary aesthetic but also for its remarkable durability and low-maintenance properties. It's eco-friendly too, reducing the need for additional flooring materials and eliminating frequent replacement cycles common with carpet or tile.
However, polished concrete isn’t a one-size-fits-all solution. The exact methods, materials, and techniques can vary greatly based on the desired look, level of gloss, aggregate exposure, and overall project goals. Understanding these nuances upfront allows architects and designers to communicate clearly in their specifications and achieve exactly the floor their clients envision.
Now, let’s get into the specifics of concrete mix design—an essential foundation for a successful polished concrete project.
2. Key Considerations for Concrete Mix Design
One of the most fundamental yet overlooked elements when specifying polished concrete is selecting the correct concrete mix. The reality is that not all concrete is created equal—especially when the goal is a flawless polished surface that retains its beauty and performance over years of commercial use. Mistakes made here can lead to uneven finishes, poor durability, and unexpected repair costs down the line.
When specifying concrete for polishing, architects should prioritize a low water-to-cement ratio—ideally around 0.40 to 0.45. Why is this important? A lower water content produces a denser slab, resulting in increased hardness, durability, and resistance to staining and cracking. On the other hand, a high water-to-cement ratio may simplify the initial pouring and finishing but can cause the slab to become weak, porous, and more susceptible to surface imperfections once polished.
Another key factor is ensuring consistency in aggregate type and size within your concrete mix. Uniform aggregates provide more predictable aesthetics, helping architects achieve their desired decorative effects—whether that's a subtle cream finish or a dramatic full aggregate exposure. We recently worked with a commercial client in St. George who initially opted for a standard concrete mix without specifying aggregate consistency. Unfortunately, the uneven aggregate distribution created an irregular, patchy finish. Correcting this required extensive grinding, adding both cost and delays to the project.
For commercial polished concrete applications, specifying concrete strength between 3,500 and 4,000 PSI is ideal. This strength level provides excellent durability and wear resistance, ensuring the polished concrete floors stand up to heavy foot traffic, furniture, and equipment over time. At Ayala’s Concrete Designs, we routinely advise architects to include these strength specifications clearly in their project documentation to avoid unnecessary repairs and maintenance.
In short, the right concrete mix sets the stage for successful polished concrete flooring. Taking the extra time to specify these critical details ensures your flooring not only meets client expectations but exceeds them for years to come.
Next, let's examine how to specify aggregate exposure and finish levels clearly, ensuring the final appearance matches your design vision.
3. Choosing the Right Level of Aggregate Exposure and Finish
One of the biggest points of confusion architects and designers run into when specifying polished concrete is clearly defining the desired aggregate exposure and finish level. Polished concrete can range from subtle, smooth, and understated to dramatically decorative—depending entirely on how deeply the concrete surface is ground, and how extensively aggregates are exposed. Miscommunication here can lead to significant misunderstandings between the client, architect, and contractor.
There are four primary aggregate exposure levels to consider:
Cream Finish (Minimal Exposure):
Achieved with minimal grinding, this finish provides a smooth, consistent surface without exposing aggregates. It’s ideal when architects prefer a clean, uniform aesthetic, perfect for modern office spaces or minimalist designs.Salt-and-Pepper Finish (Light Exposure):
This look involves slightly deeper grinding to expose fine aggregates evenly across the surface. It’s subtle yet visually engaging, perfect for retail spaces, cafes, and commercial interiors aiming for contemporary appeal.Medium Aggregate Exposure:
This approach reveals moderate-sized aggregates throughout the surface, adding visual depth and texture. It's particularly effective in larger spaces where a dynamic appearance can enhance the overall design concept.Full Aggregate Exposure:
For projects demanding a highly decorative and striking look, extensive grinding exposes large aggregates fully. Hotels, high-end restaurants, or retail showrooms often favor this finish to create visually captivating floors that make a memorable impression.
Equally important as aggregate exposure is the selection of the right gloss level. Polished concrete can range from matte (low gloss), satin (medium gloss), to high-gloss finishes. For commercial spaces, matte or satin finishes often provide a great balance of aesthetics and slip resistance, while high-gloss floors can dramatically elevate the appearance of luxury spaces, though requiring additional slip-resistance considerations.
For example, Ayala’s Concrete Designs recently completed a polished concrete project for a high-end boutique in St. George that initially lacked clarity in the specifications. The client envisioned a luxurious, full-aggregate, high-gloss finish but initially specified only “polished concrete floors.” Early discussions and clear specification updates saved the client significant headaches, ensuring the final result perfectly matched their upscale design intent.
To avoid costly misunderstandings, clearly detail aggregate exposure and finish levels in your specifications—and always request mock-ups or samples. Clear visuals ensure client expectations align precisely with the intended result.
Next, we’ll discuss moisture control and why it's an essential factor to specify upfront to protect your polished concrete investment.
4. The Importance of Specifying Moisture Control & Vapor Barriers
When specifying polished concrete flooring, architects and designers often overlook the hidden issue that can quickly sabotage even the most thoughtfully designed floor—moisture. In fact, inadequate moisture control remains one of the most common reasons polished concrete floors fail, especially in commercial projects. Moisture problems can manifest as cloudy patches, white powdery deposits known as efflorescence, or even delamination of protective treatments and sealers.
While St. George, Utah, is known for its relatively dry climate, seasonal rain, and temperature fluctuations can lead to unexpected moisture migration through concrete slabs, causing headaches long after the project wraps up. Many architects mistakenly assume that polished concrete's dense, sealed surface is enough protection, only to realize later that internal moisture issues were overlooked during specification.
A practical example is a recent polished concrete project completed by Ayala’s Concrete Designs at a local retail space. Initially, moisture testing wasn’t conducted because the project was located in a typically dry area. After heavy seasonal rains, moisture rising through the slab caused discoloration issues, requiring costly remediation. This mistake not only delayed the store opening but significantly impacted project budgets.
To avoid moisture-related problems, architects and designers should always specify moisture testing procedures as part of their polished concrete specs. Testing methods like ASTM F2170 (relative humidity testing) or ASTM F1869 (calcium chloride tests) offer reliable results, allowing you to proactively address potential moisture concerns.
Additionally, consider specifying a high-quality vapor barrier beneath the slab—typically a polyethylene barrier of 10-15 mil thickness—to further prevent moisture from rising and damaging the polished surface. While some may initially see vapor barriers as an unnecessary expense, the upfront investment is minimal compared to the cost of remediation down the road.
Clearly specifying moisture testing and vapor barriers in your design documents eliminates guesswork, reduces potential liabilities, and ensures the polished concrete floors you envision are exactly what your clients receive—beautiful, durable, and trouble-free.
Next, we'll cover another critical aspect often overlooked: effectively specifying and managing concrete cracks and control joints.
5. Properly Accounting for Joints, Cracks, and Imperfections
A frequent misconception architects and designers have when specifying polished concrete is assuming the surface will naturally hide or eliminate existing cracks or imperfections. Unfortunately, polishing a concrete slab doesn’t conceal imperfections—it often accentuates them. In other words, if cracks and joints aren’t thoughtfully addressed in your initial design and specifications, your project may face costly corrections or a final floor appearance far different from what your client expects.
Concrete inevitably cracks—this is just a fact of the material. Control joints are intentionally placed to guide cracking in a controlled manner, but accidental cracking can still occur. A few minor cracks might enhance an industrial or rustic aesthetic, but uncontrolled cracks can undermine the floor’s durability, function, and visual appeal.
For instance, Ayala’s Concrete Designs was recently brought in to repair a polished concrete floor in a St. George office building. The initial architect hadn’t specified how joints and cracks would be treated, assuming the contractor would handle this during polishing. As a result, once polished, cracks stood out sharply against the otherwise smooth finish, prompting costly last-minute repairs and patchwork that compromised the clean, modern look.
Here’s how you can proactively handle cracks and imperfections:
Specify Decorative Saw-Cut Patterns:
By incorporating deliberate saw cuts into your design, you can strategically manage cracks, guiding them into visually appealing patterns that blend seamlessly with the polished surface.Use Joint Fillers Appropriately:
Clearly specify high-quality joint fillers (epoxy or polyurea) in your plans. These fillers stabilize joints and cracks, and can be color-matched or tinted to harmonize with the overall flooring design.Epoxy Injection for Structural Cracks:
For deeper or structural cracks, specify epoxy injections early on to stabilize the slab and prevent further damage before polishing. This approach ensures stability and longevity.Set Realistic Expectations:
Ensure clients understand that some minor imperfections are natural and even add character to the polished concrete aesthetic. Managing client expectations upfront avoids dissatisfaction later.
By accounting proactively for joints, cracks, and imperfections in your polished concrete specifications, you prevent costly rework, improve the floor’s durability, and ensure client satisfaction from day one.
Next, we’ll discuss specifying slip resistance clearly to comply with safety regulations and enhance the functionality of your polished concrete floors.
6. Specifying Slip Resistance and Ensuring ADA Compliance
In commercial design, aesthetics must always be balanced with practical safety considerations—especially when it comes to flooring. Architects often choose polished concrete for its sleek, contemporary appeal, but overlooking slip resistance and ADA (Americans with Disabilities Act) compliance can lead to safety risks, potential liabilities, and costly rework.
Contrary to common assumptions, polished concrete isn't automatically slip-resistant. High-gloss finishes, though visually striking, can become slippery when wet or contaminated, posing a real safety hazard in public spaces, retail environments, or commercial kitchens. For example, Ayala’s Concrete Designs consulted on a recent project in St. George—a busy restaurant that initially opted for an ultra-glossy polished finish without specifying slip-resistant additives. Shortly after opening, several customers and employees experienced slips due to spills, prompting expensive re-grinding and refinishing to enhance traction.
To proactively address these issues, architects should include explicit instructions regarding slip-resistant treatments in their polished concrete specifications:
Choose Appropriate Gloss Levels:
For high-traffic or wet areas, consider a lower gloss finish (matte or satin), which naturally provides greater traction.Specify Slip-Resistant Additives:
Include micro-aggregate treatments or anti-slip additives in the polishing process. These treatments improve traction without significantly compromising visual aesthetics.Consider Targeted Texturing:
For particularly high-risk areas (e.g., entrances, commercial kitchens, bathrooms), specify mechanical texturing or chemical etching to enhance slip resistance precisely where needed.
Additionally, clearly specifying compliance with ADA and OSHA standards is essential. Proper slip resistance is not just good practice; it's often required by regulation. Floors must meet minimum coefficient-of-friction standards, ensuring safe passage for customers, employees, and the general public. Clarifying these requirements within your specifications ensures your polished concrete floors align with both safety guidelines and design intentions.
By clearly defining slip resistance expectations, you create polished concrete floors that are not only visually appealing but also safe, compliant, and worry-free for your clients.
In the next section, we’ll look at how architects can ensure long-term satisfaction by clearly specifying maintenance requirements for polished concrete floors.
7. Properly Specifying Polished Concrete Maintenance Plans
While polished concrete is famously durable and requires significantly less upkeep compared to traditional flooring options like carpet or tile, it's a common mistake among architects and designers to assume it's maintenance-free. Realistically, polished concrete needs a thoughtful maintenance plan to preserve its beautiful finish and ensure maximum durability over the long term.
A lack of clear maintenance guidelines in your specifications can cause unnecessary confusion and frustration for clients. Recently, Ayala’s Concrete Designs consulted with a St. George retail client whose polished concrete floor had prematurely dulled and developed visible streaks. The cause? Janitorial staff were routinely cleaning the floor with harsh, acidic cleaners intended for ceramic tile, unaware that polished concrete requires gentler treatment.
To prevent this type of situation, it's essential to explicitly outline maintenance recommendations in your project specifications. Consider the following best practices:
Daily Cleaning:
Recommend routine dust mopping or microfiber sweeping to remove abrasive dirt and debris, reducing wear and maintaining the polished surface.Weekly or Monthly Deep Cleaning:
Specify the use of pH-neutral cleaning products designed explicitly for polished concrete. These products protect the floor's finish without leaving residues or dulling the surface.Clearly Specify Prohibited Cleaning Methods:
Warn explicitly against acidic, alkaline, or ammonia-based cleaning products, as these can degrade the surface polish and lead to permanent damage.Annual Maintenance Procedures:
For high-traffic commercial spaces, include a recommended schedule for periodic buffing or re-polishing. This maintains the original sheen and protects the concrete surface.
Additionally, consider providing your clients with a clear, user-friendly maintenance guide to pass along to janitorial teams. This simple step ensures long-term satisfaction, reduces maintenance costs, and safeguards your project's aesthetics and performance.
By clearly specifying an effective maintenance strategy, architects ensure that polished concrete floors remain a beautiful and practical design choice long after initial installation.
Next, let’s discuss the importance of working closely with a specialized polished concrete contractor to ensure your design vision translates flawlessly into reality.
8. Working with a Trusted Polished Concrete Contractor
As an architect or designer, you spend countless hours meticulously detailing your polished concrete specifications—yet even the best plans can falter without the right partner to execute them. Selecting a skilled, specialized polished concrete contractor isn't just about craftsmanship; it's also about ensuring your design vision translates smoothly from paper to reality. Partnering early with an experienced team like Ayala’s Concrete Designs in St. George, UT, can dramatically enhance project outcomes and reduce costly misunderstandings.
One of the most common regrets architects express is waiting too long to bring a polished concrete specialist on board. Early collaboration provides invaluable insights that can refine your specifications, streamline construction timelines, and minimize unexpected challenges during installation. A skilled contractor can proactively identify issues such as concrete mix selection errors, moisture control oversights, or unrealistic aesthetic expectations—saving considerable time and resources.
Ayala’s Concrete Designs takes pride in its strong collaboration with local architects and designers. As polished concrete specialists, the Ayala team has helped deliver numerous successful commercial flooring projects across St. George, ranging from retail stores and restaurants to office complexes and healthcare facilities. With extensive experience, Ayala’s Concrete Designs can provide reliable mock-ups, detailed pre-installation consultations, and practical, field-tested solutions tailored specifically to your project's unique needs.
By clearly specifying the involvement of an experienced polished concrete contractor like Ayala’s Concrete Designs from the outset, architects ensure their polished concrete projects are set up for long-term success, client satisfaction, and stunning results.
Finally, let's wrap up with key takeaways and how Ayala’s Concrete Designs can help bring your next polished concrete project to life.
9. Bringing Your Polished Concrete Vision to Life
Successfully specifying polished concrete for commercial projects involves careful planning, attention to detail, and proactive collaboration. Each step—from choosing the right concrete mix and defining aggregate exposure, to considering moisture control, slip resistance, and ongoing maintenance—is essential for a flawless outcome.
At Ayala’s Concrete Designs, we specialize in working closely with architects and designers to ensure your polished concrete floors meet every aesthetic, performance, and durability expectation. With years of experience supporting projects in St. George, UT, our team is ready to provide expert guidance and practical solutions tailored to your needs.
Ready to get started on your next polished concrete project? Contact Ayala’s Concrete Designs today at 435-229-7314 or email [email protected]—let’s collaborate to deliver exceptional floors your clients will love.