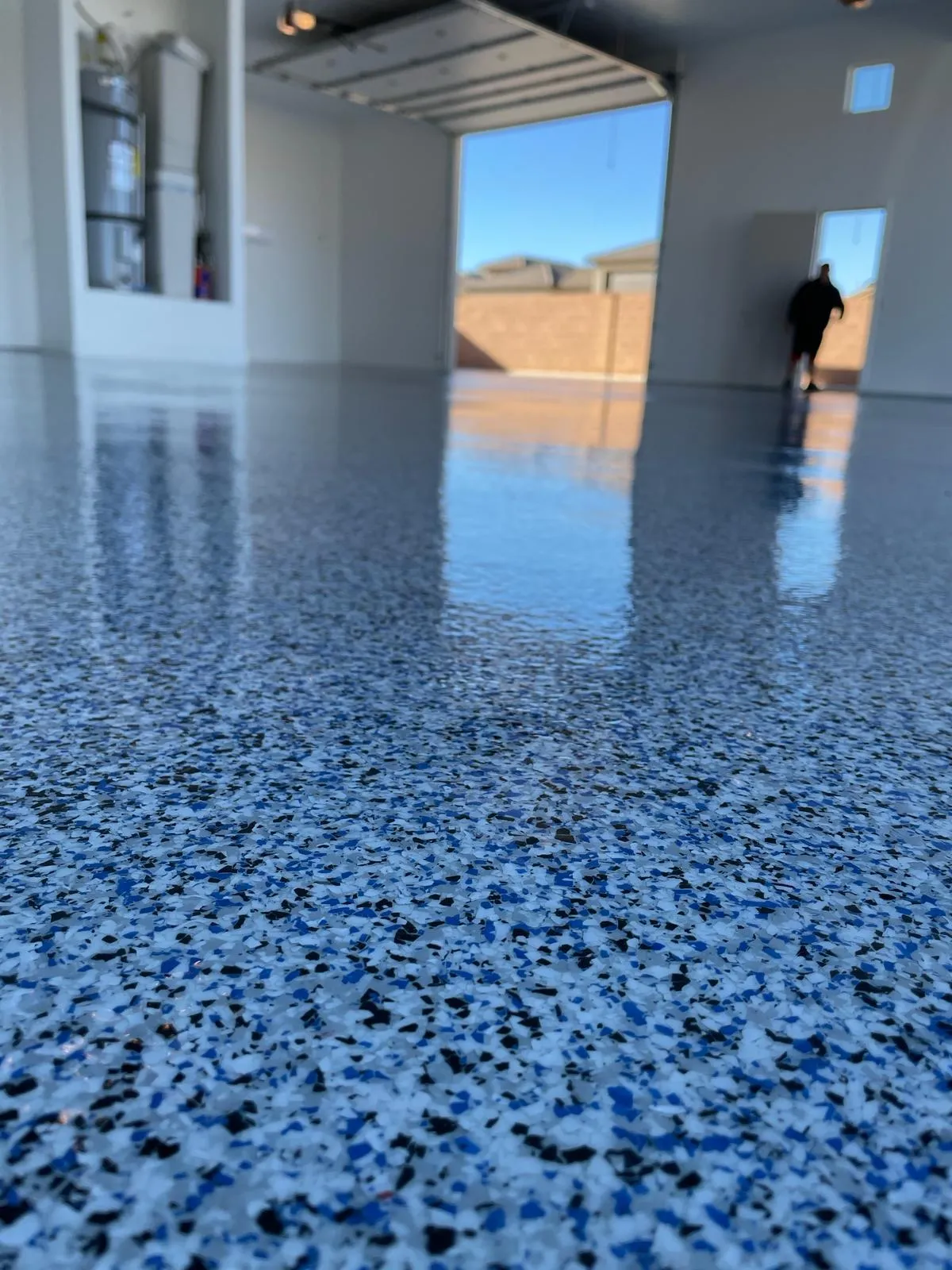
How We Prep Epoxy Floors in St. George – Ayala’s Concrete
Table of Contents
The Truth About Epoxy Floors
Why Prep Matters More Than the Product
What We Look for Before We Even Touch the Grinder
Surface Prep Step-by-Step: Our Actual Process
What Happens When Prep Gets Skipped (And How to Spot It)
Why Southern Utah’s Climate Demands Better Prep
Professional-Grade vs. DIY: The Prep Tells You Everything
Why We Do It This Way (And Don’t Cut Corners)
Let’s Walk Your Slab Together
1. The Truth About Epoxy Floors
Let’s set the record straight— most epoxy floor coatings don’t fail because of the product. They fail because the prep work was rushed, skipped, or flat-out done wrong.
We’ve seen this more times than we can count. A homeowner calls because their garage floor is peeling, or a business owner is frustrated that their brand-new flake floor is already chipping at the hot tire zones. Most of the time, the epoxy system wasn’t the problem. The problem was what it was sitting on: a slab that was never prepped to hold it.
If you’ve ever seen a contractor show up with a broom, a leaf blower, and a Home Depot bucket of epoxy, that’s your red flag. Surface prep isn’t something you can shortcut—not if you want your floor to last more than a few seasons in Southern Utah.
We don’t say that to scare anyone. We say it because we’ve torn out dozens of failed coatings that could’ve been avoided with the right prep. And when you’ve spent good money on a garage floor, shop, or patio, the last thing you want is to pay for it twice.
This post isn’t about fancy finishes or marketing hype. We’re going to walk you through exactly how we prep concrete before we ever open a bucket of epoxy. You’ll see why we take the time to do it right, what can go wrong when it’s skipped, and how to know if your slab is actually ready for coating.
Because in this business, prep is everything. And if the floor’s not ready—we don’t coat it. Simple as that.
2. Why Prep Matters More Than the Product
Epoxy coatings are only as good as what they’re bonded to—and that’s not just a saying. It’s the reality behind every peeling, bubbling, or flaking floor we’ve ever been called to fix.
The truth is, most epoxy systems on the market today are strong enough to handle heavy foot traffic, hot tires, oil spills, and shop abuse—but only if they’re applied over properly prepped concrete. When you skip that prep—or do it halfway—you might as well be pouring your money into a bucket and spreading it over dust.
We’ve seen floors fail in a matter of months because the installer didn’t grind the surface, didn’t test for moisture, or tried to coat over old paint. In one case, a shop owner paid thousands for a “garage epoxy” that started peeling the first summer. Why? The coating was fine. The slab had been power-washed and coated—no grinding, no patching, no proper profile. The epoxy had nothing to grip.
Concrete is a porous material, and over time it collects oil, grime, paint, tire residue, and even invisible contaminants like silicone overspray from car detailing. If those aren’t removed and the surface isn’t opened up mechanically, the coating has no chance to properly bond. You might get a floor that looks good for a few weeks—but once heat, humidity, and wear kick in, it’s game over.
This is why prep matters more than brand names, topcoat warranties, or how glossy the floor looks when it's still wet. If your contractor can’t explain how they’ll prepare the surface—or worse, if they tell you it doesn’t really matter—they’re cutting corners, and your floor will pay the price.
When we walk into a job, the first thing we think about isn’t what color flake you want or how shiny the finish should be. It’s what condition the slab is in—and what it’s going to take to get it ready for a long-lasting bond. Because if the prep isn’t right, nothing else matters.
4. Surface Prep Step-by-Step: Our Actual Process
Once we’ve inspected the slab and made sure it’s a good candidate for coating, we get to work. And here’s the part that most people don’t see—the real work starts long before we open a single bucket of epoxy.
1. Concrete Grinding – Not Optional
We start by grinding the surface using industrial diamond grinders—either planetary machines or smaller edge tools depending on the space. This isn’t about smoothing the surface. It’s about opening the pores of the concrete to create a mechanical profile that the epoxy can bite into. We aim for a Concrete Surface Profile (CSP) of 2 to 3 on most garage or shop floors. That’s the industry standard for epoxy adhesion.
And no, acid etching is not a replacement for grinding. It’s inconsistent, unpredictable, and not nearly aggressive enough to cut through sealers or contamination. If someone’s still using acid etch as their main prep method, they’re about 20 years behind where the industry is today.
2. Dust Control – No Shortcuts
Our grinders are hooked up to commercial HEPA vacuums that control airborne dust during grinding. If the surface is dusty or covered in micro debris, the epoxy won’t bond properly. We also do a final cleanup pass once grinding is complete—blowing out edges, hand-scraping corners, and vacuuming until the surface is as clean and dry as possible.
3. Crack Repair & Joint Filling
Once the surface is ground, we identify any cracks that need to be addressed. Not every hairline needs repair, but if the crack moves, telegraphs, or opens up under pressure, we use epoxy crack filler or urethane repair materials to seal it permanently. Expansion joints may be left open or filled depending on use-case and coating type. This step’s critical—coating over a moving crack is asking for failure.
4. Patching and Surface Leveling
If there are divots, pitted areas, or low spots, we use patching compounds or self-levelers to even out the slab. This isn’t just about looks—it affects how the coating flows and how uniform the final finish is. A floor with uneven prep will have thin spots, rough patches, and visible transitions between sections.
5. Edging – Often Skipped, Never Ignored
We grind all the way to the edges with hand tools and vacuum-assisted shrouds. A lot of contractors skip this part or try to blend the coating into unground edges. That’s how you end up with peeling borders, exposed concrete near walls, or visible failures within a year.
6. Moisture Barrier or Primer (If Needed)
If the slab has borderline moisture levels or is going to receive a metallic or polyaspartic system, we may apply a primer or moisture-blocking base coat. This step adds insurance against adhesion failure, especially in garages that get minimal airflow and big temperature swings.
We do all of this before we ever open the epoxy. Why? Because we’ve seen what happens when you don’t. A coating is only as strong as what’s under it—and we build our floors like they’re going to war. Because in this climate, sometimes they are.
5. What Happens When Prep Gets Skipped (And How to Spot It)
If you’ve ever seen an epoxy floor that looked great at first but started peeling, flaking, or bubbling just a few months in, chances are the problem wasn’t the product—it was the prep. And once the coating fails, there’s no easy fix. You can’t patch it. You can’t touch it up. You have to grind it all off and start over.
We’ve pulled up coatings that peeled up in full sheets. No bonding. No bite. Just a thin film sitting on top of the concrete like plastic wrap. In one case, a homeowner paid for a “garage epoxy” that started chipping where the car tires parked. Turns out, the installer used a $100 DIY kit with no grinding—just a power wash and a quick roll-on coat. The slab had been sealed years earlier, and they didn’t even test for it. Within weeks, the entire center section of the floor lifted.
Here’s how you can spot a rushed or poorly prepped job:
Shiny edges and dull centers: This usually means the contractor didn’t grind the edges or prepped unevenly.
Peeling in tire paths or near door thresholds: These high-friction zones are the first to fail when there’s no proper profile.
Visible cracks or movement lines under the coating: Tells you they didn’t repair or treat cracks properly before coating.
Thin-looking patches or color inconsistency: Could mean they didn’t clean properly after grinding, or didn’t apply material evenly due to slab variation.
No dust control = poor bonding: If the crew leaves behind a dusty surface, you’re asking for adhesion failure from day one.
The real tragedy is that most of these failures don’t show up until after the warranty is over—if there was even a real warranty to begin with. That’s why we spend so much time on prep: because it’s the part of the job that decides whether your floor lasts a few months… or a few decades.
6. Why Southern Utah’s Climate Demands Better Prep
Coating concrete in Southern Utah isn’t like coating floors in the Pacific Northwest or back East. The environment here puts your floor under constant stress, and if the prep doesn’t account for that, your coating doesn’t stand a chance.
Let’s start with the heat. St. George regularly sees summer temps over 100°F. In garages and shops, that concrete slab can climb even higher—especially when it’s baking under direct sun all day. Hot tires roll in, press down on the surface, and if that epoxy isn’t properly bonded to the slab, it’ll start lifting. That’s called hot tire pickup, and it’s a common issue we’re called to fix. The real culprit isn’t the heat—it’s poor surface prep that couldn’t handle it.
Then there’s dust. Our dry desert air is full of it. If a floor isn’t properly cleaned and vacuumed after grinding, that dust acts like a release agent. The coating bonds to the debris—not the slab. A lot of coatings look good the day they’re installed. But add in wind-blown grit, UV, and daily wear, and that poor prep job starts to show fast.
We also deal with large temperature swings, especially in garages or exterior areas. Concrete expands and contracts. If cracks aren’t treated correctly, they move—and when that happens under a rigid coating, it leads to spider cracks, lifting, and failure at the joints.
And while we don’t get much snow in St. George, moisture can still creep in from poorly insulated slabs or from irrigation on patios. If the prep didn’t include proper vapor testing or the right basecoat, that moisture will break the bond from below.
We’ve seen coatings fail here that would’ve lasted years in a milder climate. That’s why we build every floor with local conditions in mind—right down to the moisture content, the way the slab is poured, and how much UV exposure the surface gets.
This isn’t just epoxy. This is desert-proof flooring—and it starts with desert-aware prep.
7. Professional-Grade vs. DIY – The Prep Tells You Everything
A lot of people think the difference between a DIY epoxy job and a professional install is the product. It’s not. The real difference is in the prep.
We’ve seen homeowners drop $200 on a kit from a big box store, watch a few YouTube videos, and roll it out over a weekend. The label says it’s durable, the photos on the box look good, and for the first week or two, it might even seem like it worked. But without mechanical prep, that coating has no real grip. It’s sitting on the slab like a sticker—and it’s only a matter of time before it peels, flakes, or lifts under pressure.
The same goes for some so-called “professionals” who charge low prices by skipping the hard parts. No grinding. No dust control. No crack repair. Just a quick wash and a shiny topcoat. It might look decent on install day, but we’ve pulled up those floors in full sheets a few months later.
A true professional-grade coating system starts with aggressive surface prep—diamond grinding, full edge detailing, vacuum recovery, and substrate analysis. You can’t fake that with a mop and bucket.
The prep tells you everything about the contractor. If they’re not grinding, they’re not building a real floor. If they don’t test for moisture, they’re guessing. If they can’t explain why CSP matters or what sealer system they’re using, they’re not doing this at a serious level.
When you walk into a finished epoxy job, you might not be able to tell what kind of prep was done—but the floor will tell you soon enough. One will last. The other won’t. That’s the difference.
8. Why We Do It This Way (And Don’t Cut Corners)
We don’t prep concrete like this because it’s easy. We do it because it’s the only way we can guarantee a floor that holds up the way it should.
There’s no shortage of quick-in, quick-out epoxy contractors out there. They offer a low price, skip the hard steps, and move on before the floor starts falling apart. That’s not how we work. When we prep a slab, we’re thinking five years ahead—not just about how it looks tomorrow, but how it’s going to hold up after hundreds of hot tire passes, pressure washes, oil drips, and summer heatwaves.
We’ve built our name on jobs that don’t come back to haunt us. That means we turn down work if the slab isn’t ready. We reschedule when moisture levels are borderline. We take the time to grind edges and patch cracks, even if no one else would’ve noticed them. Because we’ve seen what happens when those steps get skipped—and we won’t put our name on a floor that’s going to fail.
Prep work isn’t glamorous. It’s not what shows up in the photos or gets posted on Instagram. But it’s what separates a good-looking floor from a long-lasting one. And at the end of the day, we’re not interested in doing this twice. We’re interested in doing it right.
That’s why our clients trust us. Not just because the floors look great on day one—but because they still look great five years later. They know we don’t cut corners, we don’t make excuses, and we don’t disappear when the job gets tough.
If you’re going to invest in a floor, invest in a team that treats the foundation like it actually matters. Because it does.
9. Let’s Walk Your Slab Together
If you’re thinking about coating your garage, patio, or shop floor, don’t start by picking a color. Start by asking one question:
Is your concrete actually ready for epoxy?
That’s what we help you figure out. Before we ever quote a job, we’ll meet you on-site, walk the slab, and show you exactly what we’re looking for—moisture levels, surface condition, cracks, past coatings, everything. We’ll explain what kind of prep your floor really needs and whether epoxy is even the right fit. And if it’s not? We’ll tell you that, too.
No pressure. No fake urgency. Just honest input from people who’ve been doing this for over 25 years in St. George and all over Southern Utah.
If we move forward, you’ll know exactly what to expect from start to finish. If we don’t? You’ve still got solid advice and a better understanding of what makes a floor last in this climate.
Want a floor that doesn’t just look good but actually holds up? Call us. Let’s walk your slab together and make a plan that’s built to last.
Bonus: Frequently Asked Questions
1. Why is surface prep so important for epoxy floors?
Because epoxy is only as strong as what it sticks to. If the surface isn’t prepped right—meaning it hasn’t been mechanically ground, cleaned, and opened up to the correct profile—it won’t bond. It might look good for a few weeks, but it’ll start peeling, bubbling, or lifting soon after. In our experience across Southern Utah, 90% of failed coatings we’re called to fix come down to poor prep, not bad materials.
2. Can I just power wash the concrete before applying epoxy?
No. Power washing doesn’t remove embedded contaminants like oil, tire plasticizers, old paint, or invisible sealers. And it doesn’t roughen the surface to the correct CSP (Concrete Surface Profile) required for epoxy to adhere. We never rely on water for prep—we use diamond grinders, commercial vacuums, and proper testing. Anything less is a shortcut.
3. What happens if you coat over a sealed or painted slab?
It fails. Period. If there’s any type of sealer, wax, or paint on the concrete—even if it’s barely visible—it blocks the epoxy from bonding. We test every slab before grinding and make sure we’re down to clean, raw concrete. We’ve removed a lot of glossy coatings that were applied right over sealed surfaces and failed within months.
4. How do you test for moisture in concrete before coating?
We use two methods depending on the situation: a moisture meter or calcium chloride test. These let us know how much vapor is moving through the slab. If a floor is still pushing moisture, especially in garages or patios, we’ll either recommend a moisture mitigation system or pause the job entirely. Coating over a wet slab is asking for delamination.
5. Do all epoxy floors need grinding, or just older slabs?
Every slab needs grinding—old, new, residential, or commercial. Even brand-new concrete has to be profiled for epoxy to bond properly. The only thing that changes is how aggressive the grinding needs to be. Older slabs may need crack repair or leveling, but new slabs still need mechanical prep.
6. Can I use acid etching instead of grinding?
No—and any contractor who recommends that isn’t doing it right. Acid etching is outdated and unreliable. It doesn’t create a consistent surface profile, and it can actually seal off parts of the concrete if it reacts unevenly. We use diamond grinding, not acid, because it gives us full control over the prep process and results.
7. What does CSP 2–3 mean in epoxy floor prep?
CSP stands for Concrete Surface Profile, and it refers to how rough the concrete surface is after grinding. A CSP 2–3 is the sweet spot for epoxy—it’s textured enough to allow mechanical bonding without being overly rough. It’s like sanding before you paint. If the surface is too smooth or too slick, the epoxy won’t adhere, and the floor will fail.
8. How long does surface prep take before you can install the coating?
It depends on the size and condition of the floor, but most residential prep takes half a day to a full day. Larger commercial projects or heavily damaged slabs may take longer. We never rush prep—it’s the single most important part of the process. If we don’t get the prep right, nothing else matters.
9. Do you fill cracks or patch holes before coating?
Absolutely. After grinding, we repair visible cracks using epoxy filler or urethane-based materials designed for movement. We also patch spalls, pits, and low spots to create a smooth, even surface. These repairs aren’t cosmetic—they’re structural. If you coat over active cracks or damage, you’ll see it telegraph through the coating later.
10. Can I recoat over an old epoxy floor if it’s peeling?
Not without removing the failed coating first. If the old epoxy is lifting, flaking, or separating from the slab, it has to be fully ground off down to bare concrete. Coating over a bad base just traps the problem underneath. Once it’s removed, we can start fresh and give you a floor that bonds properly and lasts.