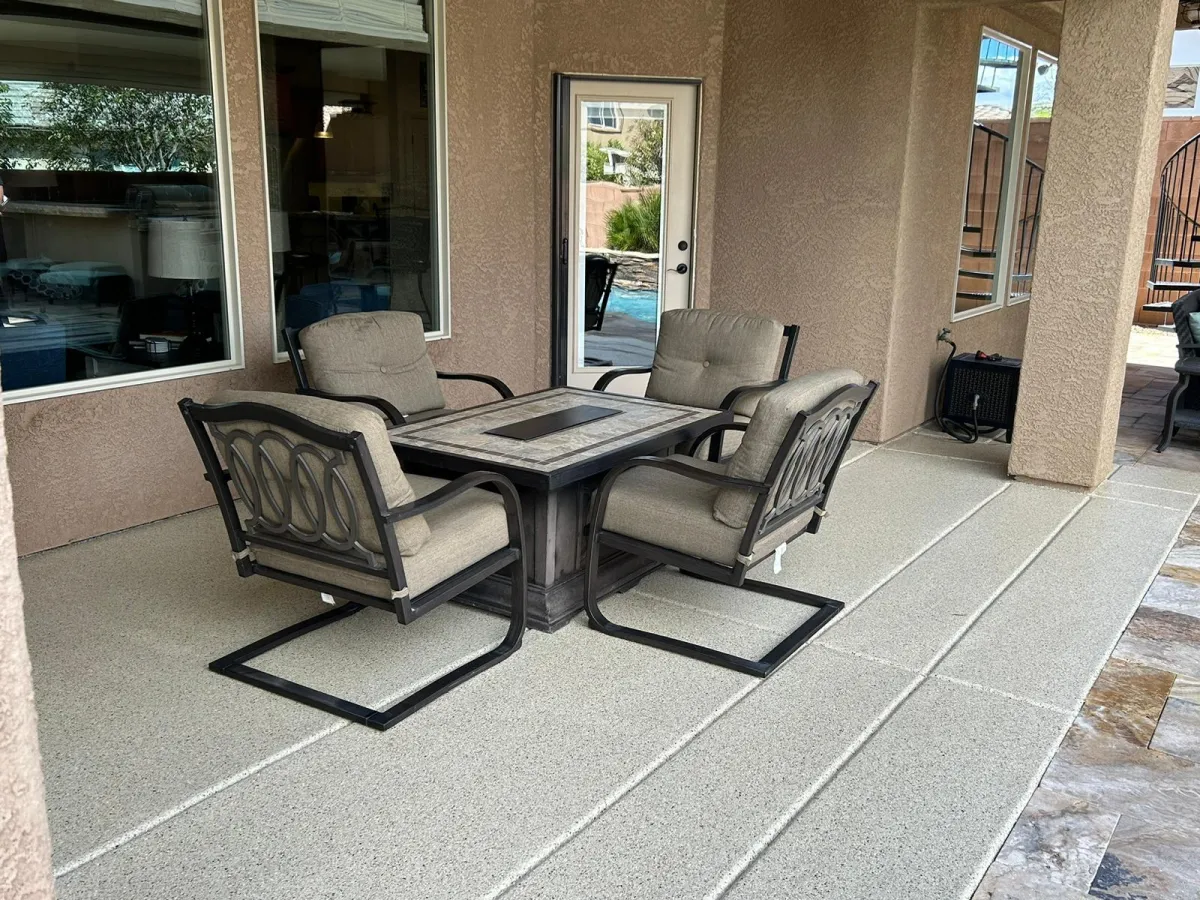
Epoxy Flooring in St. George, UT: Which Surfaces Can Epoxy Be Applied Over?
“Innovation distinguishes between a leader and a follower.” Steve Jobs might have been talking about technology, but his words also apply to home and commercial improvements—especially flooring. St. George, UT, is a place where forward-thinking construction meets scenic desert landscapes. It’s a region of rapid growth, diverse architectural styles, and a climate that tests the durability of any floor. Epoxy flooring has emerged as one of the leading solutions for garages, commercial spaces, patios, and more. There’s something about its glossy finish and industrial-grade resilience that resonates with homeowners and businesses alike.
In this deep-dive article, we’ll explore which surfaces can successfully host epoxy, the proper methods for prepping each surface, and how to decide between overlaying an existing floor or stripping everything down to the substrate. We’ll also look at real-world challenges—like dealing with heat and occasional humidity—and we’ll discuss why Ayala’s Concrete Designs in St. George stands out as a local expert. Expect a blend of technical insight, practical advice, and a conversational style that’ll make you feel confident about your epoxy flooring decisions.
Epoxy Over Bare Concrete
Bare concrete is the undisputed champion substrate for epoxy. When you’re in the middle of a new build or a major renovation, having unobstructed access to the raw slab gives you the chance to create the best possible bond. That’s because epoxy thrives on direct contact with a well-prepared concrete surface. The pores in the concrete offer tiny pockets for the epoxy to grab onto, forming a mechanical bond that’s incredibly strong.
Part of prepping bare concrete involves mechanical abrasion—usually via grinding or shot blasting—plus a thorough inspection for cracks or damage. St. George’s climate can be dry and hot, which sounds like it would be ideal for installing epoxy, but dryness doesn’t automatically guarantee no moisture in the slab. Testing for moisture vapor transmission is still essential. If the slab emits too much vapor, it can push the epoxy away from the concrete once the coating cures.
When everything checks out, applying an epoxy primer can seal the slab and ensure the topcoat lays down smoothly and uniformly. Skipping a primer might save a few dollars in the short term, but it often sacrifices long-term durability. In high-traffic areas—like garages that deal with car tires, golf carts, or even your annual house party—every little step that improves bond strength pays off.
The payoff is a floor that’s a breeze to clean, resistant to chemicals, and up to the task of handling heavy foot or vehicle traffic. The main downside is that any existing flaws in the slab—like deep cracks—must be repaired first, or they could telegraph through the epoxy layer. That’s a fixable issue, though. In most cases, nothing beats the direct application of epoxy onto bare, properly prepared concrete.
Epoxy Over Existing Coatings
Maybe you bought a home or commercial building that already has some sort of coating on the concrete. It could be paint, sealer, or even a dated epoxy layer that’s worse for wear. Often the decision to apply new epoxy over the old depends on whether the existing layer is solidly adhered. If it’s peeling or flaking in multiple areas, it’s better to remove it altogether.
If it is stuck on firmly, you can perform a cross-hatch test or a pull-off test to confirm adhesion. Successful results there mean you can scuff the surface to create texture and then apply a new epoxy system. This route saves both time and disposal costs. The risk is that if there’s a hidden weak spot beneath the old coating, your new epoxy might fail prematurely.
In St. George, the dry climate can sometimes lead to older coatings getting brittle and cracking over time. If you see those signs, consider at least partial removal. A professional contractor like Ayala’s Concrete Designs can help you determine what’s salvageable and what’s not. If they say it’s good to go, you can overlay with confidence. If they say it’s time to strip it off, trust that they’re saving you from an even bigger headache down the line.
Epoxy Over Tile
Tile floors are common in many southwestern-style homes, as well as commercial kitchens or restaurant settings. The question is whether you can epoxy over that tile without removing it. The short answer is yes—if the tile is firmly attached and the grout lines are in decent shape. However, you’ll need to address potential issues like cracked or hollow-sounding tiles, because those indicate potential instability.
Surface prep involves cleaning the tile thoroughly. Kitchen tiles, for example, can accumulate grease and other residues that would hinder epoxy bonding. You also need to abrade the tile’s glossy surface by grinding or sanding. Grout lines should be cleaned out and filled with an appropriate epoxy patch or leveling compound if you want a smooth final finish.
Many people opt to install epoxy over tile instead of ripping it up to avoid the noise, debris, and cost of demolition. This is a big plus if you’re renovating a commercial space that can’t afford long closures. The main caveat is that tile is a rigid surface, so if there’s any underlying movement or moisture, you might see problems later. For stable tile floors in good condition, though, epoxy can be a time-saving solution that delivers a dramatic visual upgrade.
Epoxy Over Vinyl
Commercial spaces often have vinyl composite tile (VCT) or sheet vinyl that’s past its prime. Epoxy can bond well to vinyl as long as the vinyl is well-adhered to the subfloor. If corners or edges are curling, you may need to remove or patch those sections. The top surface of the vinyl should be lightly sanded or scuffed to allow the epoxy to grip. It’s also critical to remove all traces of wax or polish.
Some older vinyl floors contain asbestos, so in older buildings, it’s important to do a proper inspection or consult experts in abatement. If the vinyl passes all these checks, epoxying over it can be a shortcut that avoids the cost of hauling away old flooring. The risk is that if the adhesive holding the vinyl to the subfloor is weak or deteriorating, it can come loose eventually and take your epoxy floor with it.
Epoxy Over Wood
You might think wood and epoxy don’t mix, but it’s possible to achieve a stable bond if the wood subfloor is thoroughly secured and moisture content is strictly controlled. Wood naturally expands and contracts with changes in humidity, which can stress rigid materials like epoxy. If you’re set on epoxying a wood floor—maybe you’re going for a specific design effect—be prepared to install a rigid underlayment or use special primers to account for subtle movement. Many contractors suggest you fix any squeaks or structural issues first, then sand the surface to create texture for epoxy. In a desert-like environment, you might have fewer issues with humidity swings, but you still want to be cautious.
Epoxy Over Metal
Metal surfaces in industrial or specialty settings can also receive epoxy. It’s essential to remove any rust, old paint, or oil and to create a rough surface profile. Sandblasting is a common approach. Once that’s done, a metal primer that’s epoxy-compatible is typically applied before the final floor system. This method helps industrial facilities reduce corrosion and makes floors easier to clean. The big watch-out is vibration or flex in the metal, which could crack the epoxy. If the metal floor is used for heavy machinery, consult a contractor who’s done metal epoxy projects and can account for all those dynamic stresses.
Prep Work: Don’t Skimp
Regardless of substrate, prep work is the single most important factor in any epoxy job. You want to confirm there are no hidden moisture issues, thoroughly clean and degrease, repair cracks or spalling, and create the correct surface profile for epoxy to latch onto. Low spots, high spots, or structural problems need to be addressed. Some folks assume that a thick epoxy pour will even out all those flaws. It won’t. Epoxy follows the contours of your existing floor like a second skin, so you need to fix them before you pour.
You also need to consider temperature and humidity when applying epoxy. In St. George, UT, summers can be scorching, and that heat can actually speed up epoxy’s pot life (the time you have to work with the mixed resin before it starts to harden). The dryness can help with curing in some ways, but you still need to be vigilant about direct sunlight or extreme temperature swings, as they can cause the epoxy to set unevenly or develop bubbles.
Pros and Cons: Overlay vs. Removing the Floor
If your existing floor is stable, overlaying epoxy can be a huge time- and money-saver. You get to skip the demolition phase, which can be dusty, loud, and disruptive. You’ll also reduce waste going to the landfill. The potential downside is that you’re rolling the dice on the existing surface. If it has any hidden problems—like moisture intrusion, weak adhesive, or unseen cracks—those issues could compromise your new epoxy. Think of it like painting over old paint that’s not fully adhered. It might look fine for now, but any underlying weak spots eventually show through.
Going down to the bare substrate removes guesswork. You’ll see exactly what shape the slab is in, make any repairs, and apply your epoxy directly to a stable base. This approach tends to yield the most robust, long-lasting installation, but it’s more expensive up front and takes more time. The choice boils down to your budget, timeline, and how risk-averse you are about potential failures in the future.
Practical Tips for St. George Property Owners
For many residents and business owners in St. George, the climate is a double-edged sword. You get plenty of sunshine, which is wonderful but can also lead to high slab temperatures in garages or external areas. Consider the time of year you start your epoxy project. Mid-summer might make epoxy set faster than you’d like, while cooler months can allow a more controlled cure. That said, your contractor can often work around these conditions with specialized formulations or by adjusting the timing of the pours (like early morning application).
Also, think about the final design. Epoxy comes in a range of options, from solid colors to decorative flake broadcasts, metallic pigments, and even custom patterns. Communicate your aesthetic goals with Ayala’s Concrete Designs so they can recommend the right epoxy system and topcoat. If you’re going for a showroom-style metallic swirl, that might require different prep or a different layer thickness than a standard gray garage coating.
Finally, always respect cure times. Epoxy floors can feel dry to the touch within a day, but full chemical cure can take several more days. Jumping the gun and parking your car or placing heavy furniture too early could lead to impressions or permanent marks in the coating.
Why Ayala’s Concrete Designs in St. George, UT?
If you’re in St. George, you have a few local options for epoxy installation. So why partner with Ayala’s Concrete Designs? The simple answer is proven expertise. They live and work in this area, which means they know exactly how the dry heat of Utah affects concrete, adhesives, and epoxy resins. They understand local building trends, common slab issues, and the questions that keep property owners up at night.
On top of the technical know-how, they pride themselves on personal service. They’ll walk you through moisture testing, help you decide whether overlaying is safe or if removal is worth the investment, and guide you through design choices that fit your style and budget. Their goal is to leave you with a floor that’s both gorgeous and built to handle day-to-day demands. They also keep you looped in on scheduling and progress, so you’re never left guessing when the next phase will start or finish.
Ultimately, choosing a local specialist means you’re investing in quality and accountability. If you have any concerns or need maintenance tips down the road, you won’t be chasing a company in another city or state. With Ayala’s Concrete Designs, you get a neighborly handshake along with professional results.
Epoxy flooring might look sleek and simple on the surface, but there’s a world of complexity beneath that glossy exterior. Different substrates—concrete, tile, vinyl, wood, metal—each come with their unique preparation needs. You can often overlay on an existing floor, which saves time and cost, but only if that floor is solid and free of hidden problems. If you have any doubts, stripping down to the bare substrate offers the highest odds of success, especially if you want the floor to endure for the long haul.
What’s universal in every scenario is the need for meticulous prep. That’s why you hear so many pros say that 80% of the work is in getting the floor ready, and only 20% is the actual pouring or rolling of epoxy. This approach ensures you don’t end up with ugly surprises or a coating that peels the first time the weather changes or someone drops a wrench on it.
St. George residents and business owners deserve top-quality floors that match the region’s beautiful desert vibes. With an experienced partner like Ayala’s Concrete Designs, you’ll have the confidence that your epoxy floor will stand up to daily wear, seasonal shifts, and the occasional experiment with leaving your car’s AC blasting on a scorching summer day. Epoxy is a worthwhile investment if done right, and now you have the insider knowledge to guide your decisions.
Contact Information for Ayala's Concrete Designs
If you’re ready to discuss your epoxy flooring plans, you can call 435-229-7314 or email [email protected] We will be happy to answer any questions or set up a consultation.