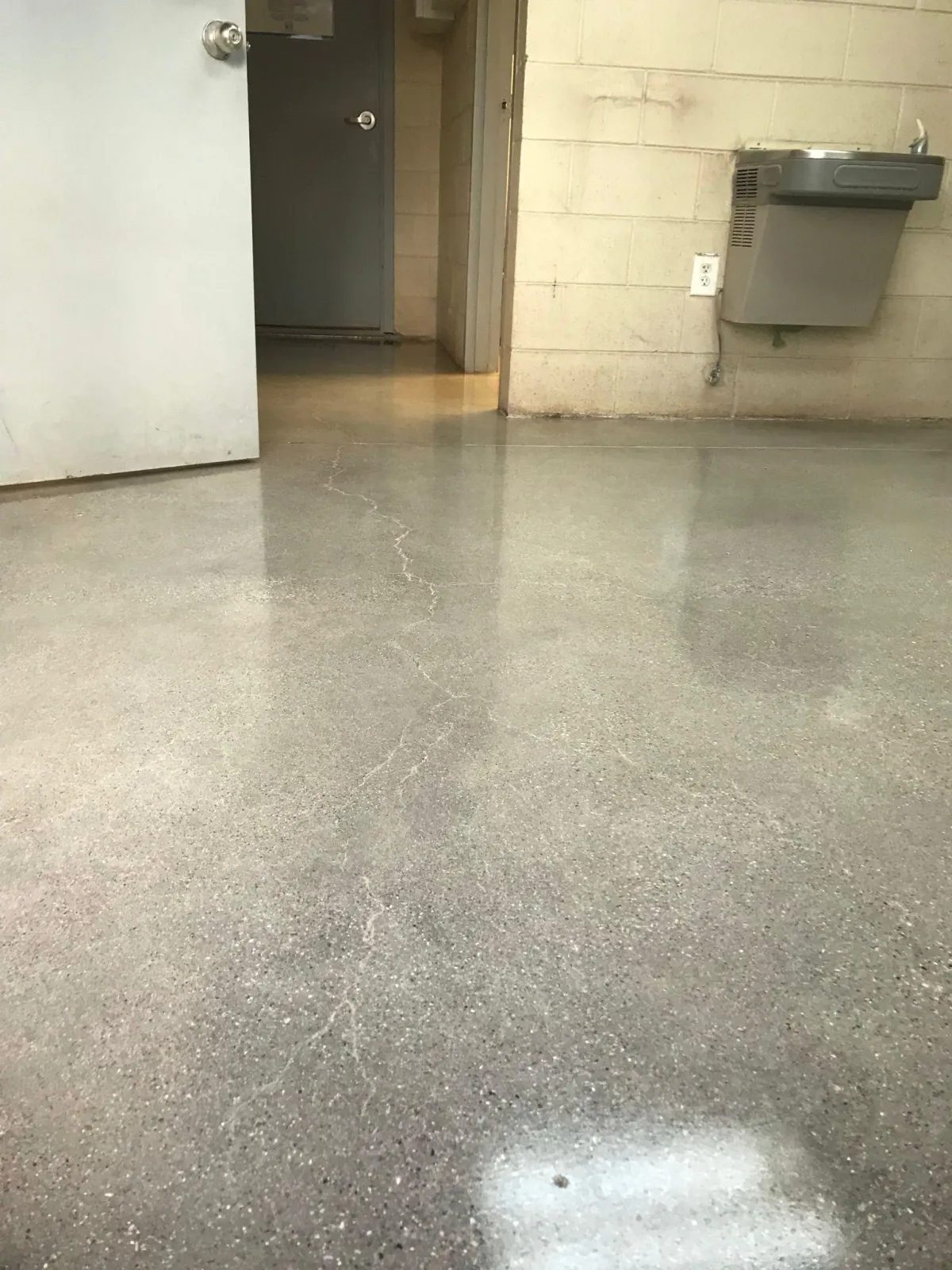
Polished Concrete Sealers in St. George: Protecting Color, Boosting Brilliance, and Extending Floor Life
St. George’s warm desert air and scenic red rocks create a spectacular backdrop for architectural innovation. It’s no wonder so many local homes and businesses have turned to polished concrete to blend modern flair with sturdy, low-maintenance functionality. Yet even in a place where the sun shines most days, polished concrete floors face plenty of challenges—abrasive dust, temperature swings, and the threat of spills or chemical exposure.
One experienced flooring pro once told me, “Polished concrete can be a lifetime surface, but only if you seal and protect it like a prized possession.” That stuck with me. You see, the very act of polishing densifies and smooths out the slab, but there are still micro-voids waiting to trap dirt or moisture. A specialized sealer for polished concrete is the finishing touch that ensures dust, liquids, and even UV rays won’t degrade that glossy plane. Let’s walk through everything you need to know to preserve your polished concrete floors in St. George, from color retention to exterior usage, so they stand proud for years to come.
Unpacking the Basics: Why Seal at All?
Polished concrete often looks bulletproof—rock-hard, gleaming, and ready for anything. But bare polished slabs can still absorb moisture or stain over time. The densification process does strengthen the surface, yet a targeted sealer adds another layer of defense. Picture a protective film that either penetrates slightly or sits atop the surface, blocking out contaminants and slowing wear. That’s crucial if you run a business where foot traffic never stops, or a home with playful kids and pets.
With a proper sealer, your polished concrete floor also achieves a more uniform gloss. Some floors without sealers exhibit patches of uneven sheen or minor scratching in busy zones. The sealer helps even out these discrepancies, ensuring the entire surface remains consistent and vibrant. Here in St. George, dust can act like sandpaper if it’s constantly ground into an unsealed floor. Sealing ensures that dust doesn’t burrow into micro-voids, making daily cleanup much simpler.
Moreover, sealed polished concrete stands up better to those little day-to-day hazards. Drag a heavy piece of furniture, drop a tool in the garage, or spill a soda in the kitchen—your risk of permanent damage is drastically reduced. The sealer essentially acts like a high-tech shield, taking the brunt of scratches or stains so the underlying polished concrete remains pristine. Especially in a desert climate where dryness and dust can relentlessly assault surfaces, the right sealer keeps your floor looking brand new. Without it, you might see subtle scuffs multiply into a dull haze. That’s a fate no homeowner wants for their once-glossy polished concrete showpiece.
A Different Breed of Sealer for Polished Concrete
Many big-box store sealers promise water-beading or anti-spalling qualities. While fine for standard sidewalks or rough concrete, these products rarely address the unique needs of polished concrete. Sealers designed for polished floors often have acrylic or polyurethane resins that meld seamlessly with the densified layer, enhancing reflectivity and preventing premature wear. They also tend to be breathable, preventing moisture from getting trapped and causing cloudiness or flaking.
Some advanced formulas include UV blockers to keep stains or dyes from fading under the strong Utah sun. Others boast chemical resistance, important for warehouses or retail spots dealing with solvents or cleaning agents. Plainly put, a polished concrete sealer is tuned to magnify the aesthetic qualities—like color depth and gloss—while providing industrial-grade protection. St. George’s scenic, sunlit spaces deserve that extra level of performance.
Remember that polished concrete typically involves a densifier step, and not every hardware-store sealer plays nicely with densifiers. If the product is incompatible, you could get poor bonding, peeled spots, or a mottled appearance. Manufacturers of polished concrete systems usually recommend a sealer specifically tested with their densifiers or finishing compounds. That synergy ensures maximum hardness and gloss retention, which is why a random “general use” sealer might fall short. When in doubt, always check with a knowledgeable polished concrete installer or a reputable supplier who understands the chemistry behind advanced sealers.
An Artful Process of Application
Sealing polished concrete isn’t a slapdash chore. After the final polishing pass, you remove all dust and residue, ensuring the floor is immaculate. Then, you either spray or spread the sealer in a whisper-thin coat, carefully avoiding overlaps or puddles. Some products call for a high-speed burnisher pass to fuse the sealer with the micro-surface of the polished concrete, effectively melding the two layers into one highly resistant shield.
Don’t rush these steps. St. George’s air can be hot and dry, which sometimes means the sealer evaporates faster than expected. If you notice streaking or if your applicator drags, you may need to adjust your technique or the timing of coats. The best results come from slow, deliberate passes, allowing each section to settle before moving on. If done right, the floor will glisten like glass, revealing the full potential of your polished concrete.
In some cases, especially for stained or dyed polished concrete, you might apply a specialized color-lock sealer or additive prior to the main seal coat. This step ensures pigments don’t fade or bleed. Once that initial layer dries, the next coat of sealer or guard formula enhances the gloss further and solidifies chemical resistance. Each layer plays a distinct role: one focuses on color preservation, another focuses on scuff resistance, and both together perfect the final sheen. This multi-layer approach is especially beneficial if your polished concrete is in a high-profile location, such as a retail front or showroom, where aesthetic perfection matters every bit as much as durability.
Maintenance & Resealing: The Lifeblood of Longevity
No matter how robust the sealer, friction and time will eventually wear it down. The difference lies in how often you need to reapply. A residential polished concrete floor with light foot traffic might keep its luster for a couple of years before you notice any dull spots. A bustling commercial area, on the other hand, might need an annual refresh, especially if carts or large machinery cross it daily.
You don’t want to wait until the sealer is completely worn away. A quick re-coat at the first hint of wear can save you from more extensive restoration later. In between, regular dust mopping or gentle sweeping keeps abrasive particles off the surface. Mopping with a neutral pH cleaner or auto-scrubbing in commercial buildings further helps preserve sealer integrity. Treat your polished concrete floor like an asset—because that’s precisely what it is.
In St. George, dust can accumulate surprisingly quickly, and if it’s ground into the sealer, micro-scratches will begin to appear. Over time, these tiny scratches can accumulate, making the polished concrete look hazy or dull. By resealing before those scratches become too pronounced, you effectively reset the clock, restoring that glossy finish. Some businesses schedule a burnishing session every few months to touch up the top layer and buff out minor scuffs. That’s often paired with a light reapplication of a protective “guard” product. The synergy of small, regular interventions ensures that your polished concrete surfaces age gracefully, retaining the warmth and elegance they had the day they were installed.
Sealing Over Stained and Dyed Concrete
Color transforms polished concrete from an industrial-chic surface into a decorative showpiece. But color demands protection. A specialized sealer locks in those pigments, preventing UV or chemical damage. For acid-stained floors, you’ll need to neutralize any remaining acid before applying a sealer; otherwise, a chemical reaction could lead to hazing or peeling. Water-based dyes generally need less prep, but testing is still wise to confirm the sealer won’t shift the hue.
In a city like St. George, where the desert sun can be intense, you’ll appreciate UV-inhibiting sealers that shield your tinted polished concrete from noticeable fade. Colored floors also benefit from film-forming sealers that enrich the hue, making it appear more saturated. Some owners welcome that deepening effect, while others prefer a minimal color shift. Experimenting on a small area can guide you toward the look you love without unpleasant surprises.
For those aiming to layer multiple colors—say you have a base stain plus accents of a secondary dye—sealing between coats can sometimes help define the boundaries more crisply. Each layer of color is locked into the polished concrete before the next hue is applied. This technique allows for intricate patterns or faux finishes that wouldn’t be possible otherwise. The final sealer then becomes the unifying element, bridging all color layers and preserving them under a transparent, high-gloss shield. If you skip sealing between these color applications, the dyes could blend or bleed into each other, marring your artistic vision. A step-by-step sealing approach ensures the final product is as crisp and vibrant as you imagined.
For Exterior Polished Concrete: Extra Challenges
You won’t see exterior polished concrete everywhere, but it’s certainly an option in patio spaces or covered walkways here in St. George. The same rules apply, but in a harsher environment. Intense sunlight can degrade lesser-quality sealers, so pick one labeled UV-resistant or non-yellowing. Adding slip-resistant media might also be wise if water is likely to accumulate—consider the occasional desert rainstorm or moisture from nearby sprinklers.
Exterior polished concrete also tends to collect more debris—dust, sand, or even leaves that decay and stain. A strong sealer stands guard, preventing these elements from penetrating deeply. While you may need to reseal more frequently outdoors, the trade-off is a floor that maintains its allure despite Mother Nature’s unpredictability. If you’re taking the bold step of polishing an outdoor slab, don’t forget the sealing step—it’s the difference between a short-lived novelty and a lasting statement piece.
Temperature shifts matter, too. Although St. George rarely experiences harsh winters, nighttime temperatures can still dip sharply compared to daytime highs. These fluctuations can cause the polished concrete to expand and contract slightly, stressing any coating that isn’t flexible enough to handle the movement. A high-grade sealer—particularly those with polymeric backbones—can accommodate that mild flex without cracking or peeling. Skimping on quality could lead to micro-fissures in the sealer film, inviting water infiltration and eventual damage. If you prize your exterior polished concrete, invest in a sealer that endures St. George’s desert extremes without splitting under thermal stress.
Avoiding the Traps
Rushing a sealer job on polished concrete can be a recipe for expensive do-overs. A common blunder is using a random sealer leftover from some other project, not realizing it may ruin the polished effect or fail to bond. Another pitfall is ignoring the manufacturer’s instructions on coverage rates and dry times. Some folks try to apply extra-thick coats, assuming it’ll “protect better.” In reality, it often leads to milky streaks or a gummy finish.
Chemical incompatibilities also trip people up. If you used one brand’s densifier and a different brand’s sealer, you could end up with color splotches or poor adhesion. Testing a small section first might seem tedious, but it’s an insurance policy. The same goes for ignoring temperature or humidity guidelines. St. George’s hot, dry air can speed up cure times, leaving you with less working time than you’d expect. Know the product, plan accordingly, and don’t cut corners.
Then there’s the issue of timing. Some sealer formulations advise waiting a certain number of hours (or days) after the final polishing pass. Jumping the gun might trap polishing residue or disrupt the densifier’s chemical reaction. Others might specify a burnishing step immediately after applying the sealer, while it’s still in a specific tack range. Missing that window leads to an uneven bond. Each manufacturer designs their sealer to complement the intricacies of polished concrete finishing. When you deviate from those guidelines—by reintroducing foot traffic too soon or skipping recommended topcoats—you gamble with results that could undermine the entire job.
Peering Under the Hood: Sealer Chemistries
Acrylics are common in polished concrete sealing, offering decent color enhancement and a moderate level of durability. Polyurethanes step it up, resisting more abrasions and harsh chemicals.
Whichever chemistry you choose, pay attention to how it handles UV, foot traffic, and chemical exposure. Is it prone to yellowing? Does it stand up to daily scrubbing with mild detergents? In St. George, these factors aren’t hypothetical. Real life here means dusty sidewalks, bright sunlight, and occasional temperature swings. A well-chosen sealer for polished concrete helps ensure your floor remains a highlight of your property, rather than an ongoing maintenance woe.
Also consider layering strategies. Some owners start with a penetrating sealer—especially if their polished concrete sits partly outdoors or in a moist environment—then top it with a film-forming product that amplifies gloss. This dual-system approach can provide deeper moisture protection and a glossier finishing coat on top. The key is compatibility. If the penetrating layer is silicone-based, the top film-forming sealer must adhere well to that chemistry. Otherwise, you risk peeling or incomplete coverage. Talking to a local polished concrete expert can help you find a layered approach suited to St. George’s unique climate and your personal style.
Where to Turn Next
You might be reading this because your polished concrete floor no longer shines like it once did. Or maybe you’re building a new home or renovating a storefront and want to get the flooring right from the start. Either way, the sealer choice is paramount. A small investment in the right product and application can save thousands in potential re-polishing down the road.
At Ayala’s Concrete Designs, we’ve partnered with homeowners, businesses, and contractors throughout St. George to give polished concrete floors the durability and beauty they deserve. Whether you have a complex color design, an outdoor entertaining area, or just a simple polished slab that needs a protective coat, our team has the expertise. Reach us directly at 435-229-7314 [email protected]
We understand local conditions—from desert dust to scorching sunlight—and we’ll point you toward a sealer system that fits your needs. Polished concrete can be a long-term statement floor; let’s make sure it stays as vibrant and flawless as the day it was installed.