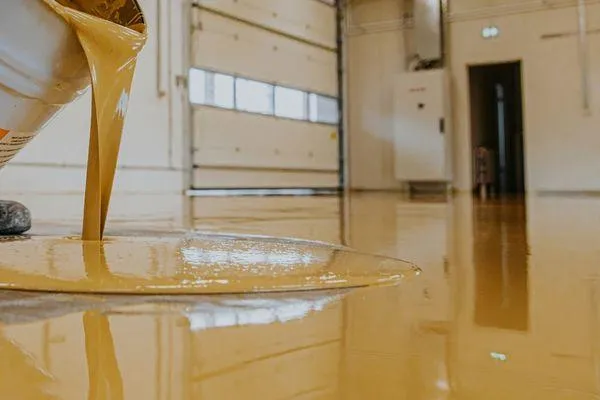
The Importance of Proper Surface Preparation for Long-Lasting Epoxy Floors
The Importance of Proper Surface Preparation for Long-Lasting Epoxy Floors
When it comes to epoxy floors, longevity and performance are key factors that depend heavily on one crucial step: surface preparation. Many homeowners and businesses may focus on the type of epoxy or the aesthetic finish, but neglecting proper preparation can lead to costly issues down the line. In this article, we’ll explore why surface preparation is critical for a durable epoxy floor and what the process entails, especially in St. George, Utah, where climate and wear-and-tear can vary greatly between residential and commercial spaces.
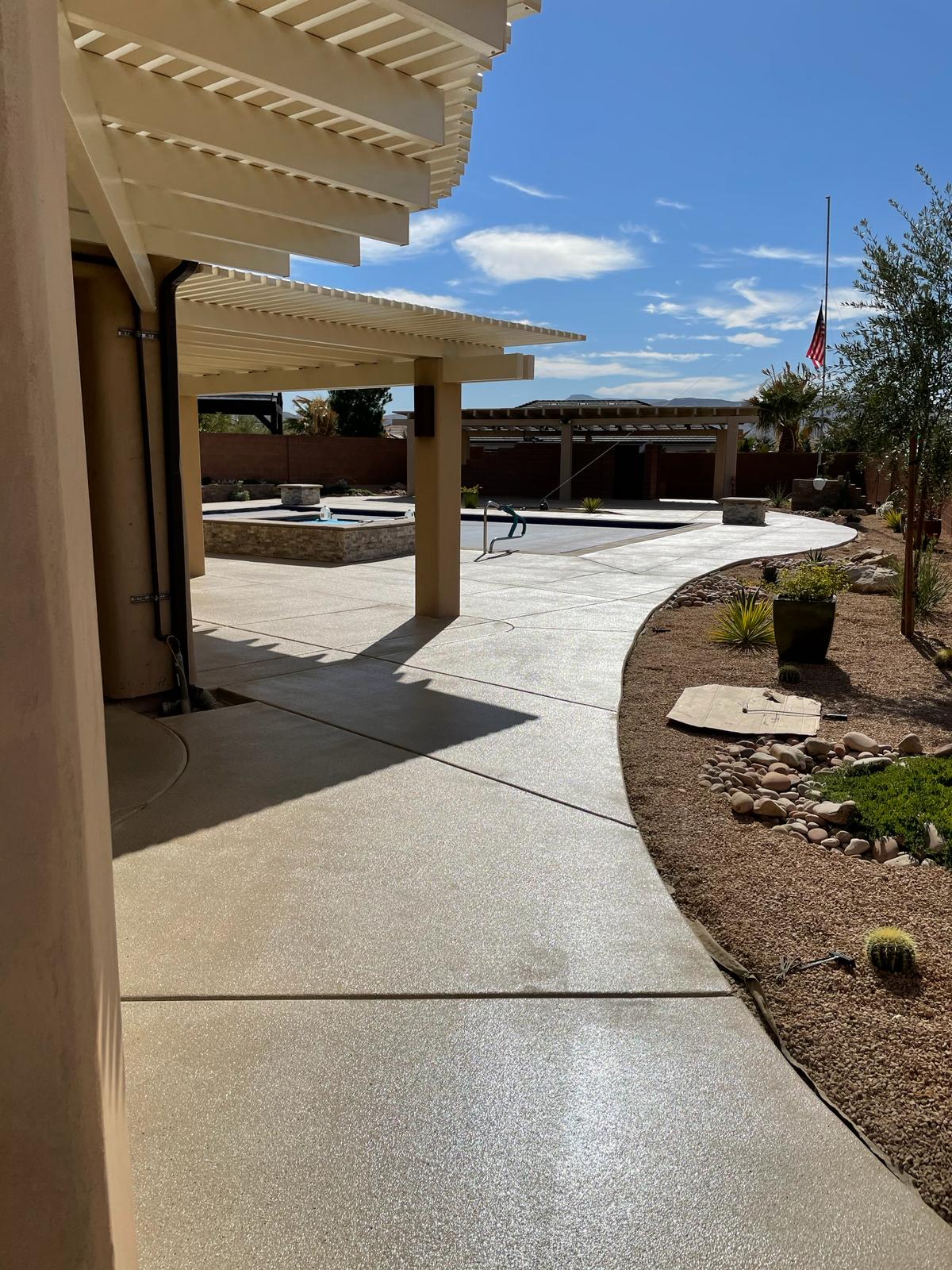
Why Surface Preparation Matters
Proper surface preparation ensures that the epoxy bonds correctly to the substrate, providing a durable and long-lasting floor. Without a clean, well-prepared surface, the epoxy may not adhere properly, leading to problems like delamination, cracks, or premature wear. For homeowners and businesses in St. George, Utah, where temperature fluctuations and moisture levels can affect flooring materials, preparation is especially crucial.
Here’s why proper surface preparation is essential:
Improved Adhesion: Epoxy coatings need to bond directly to the concrete surface to ensure longevity. Any contaminants, such as oils, dust, or old paint, can prevent proper adhesion and cause the epoxy to lift or peel prematurely.
Increased Durability: Floors that have been properly prepped can handle heavy foot traffic, impacts, and chemical spills better. This is especially important for commercial settings like warehouses, garages, or industrial facilities where the flooring takes a beating.
Moisture Mitigation: Moisture in the concrete can seep into the epoxy coating and cause bubbles, blisters, or peeling. In Utah’s desert climate, where sudden rainstorms can increase humidity, it's crucial to ensure the concrete is dry and sealed correctly.
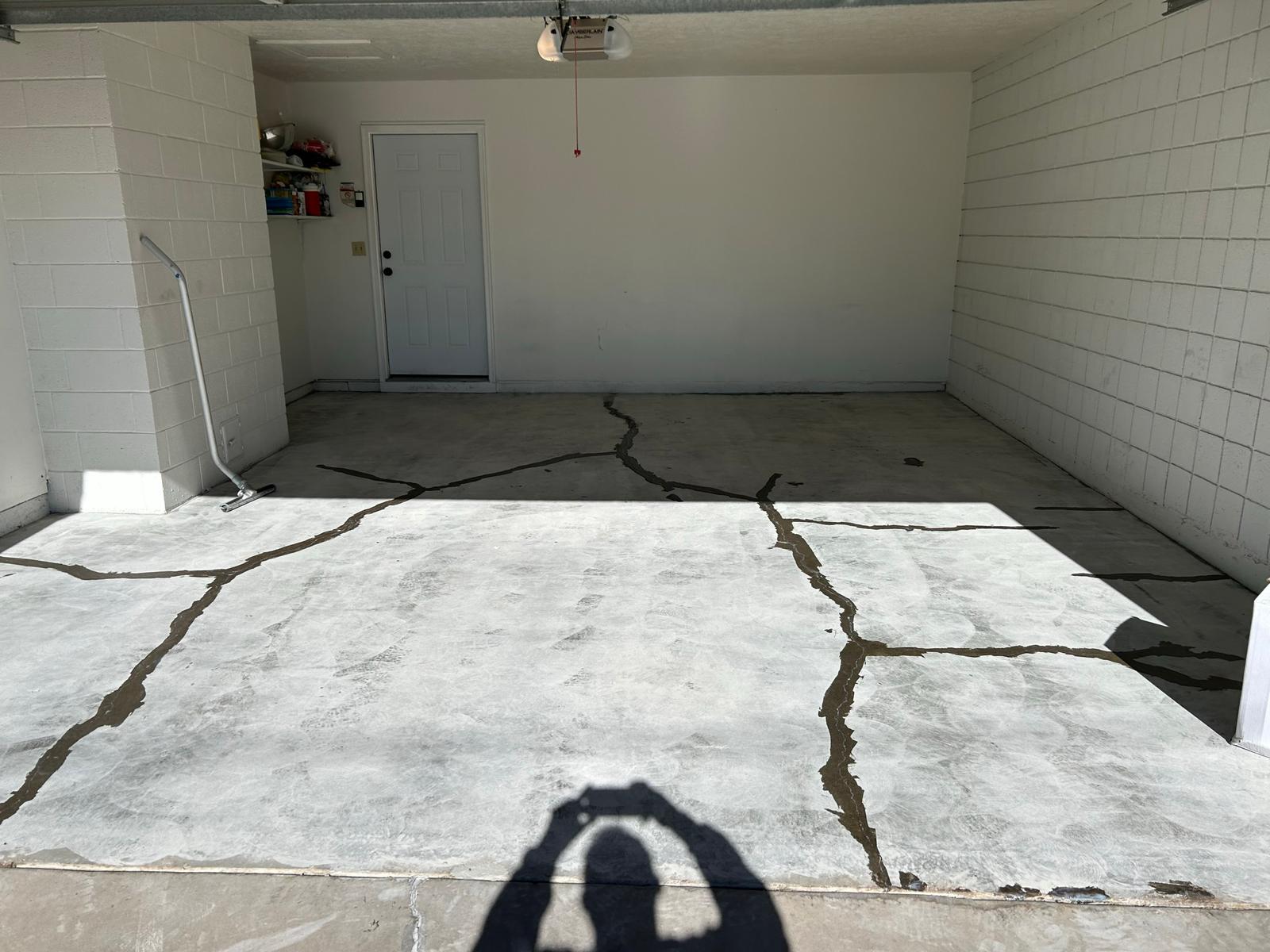
Key Steps in Surface Preparation
Surface preparation for epoxy floors isn’t a one-size-fits-all process. Each project requires careful attention to the condition of the existing concrete and the end-use of the space. Here are the key steps involved:
1. Cleaning the Surface
Before any physical preparation can take place, the surface needs to be thoroughly cleaned to remove dirt, oil, grease, or other contaminants. In commercial spaces like restaurants or auto shops, where spills are common, this step is particularly important. A clean surface ensures that nothing interferes with the bond between the epoxy and the concrete.
2. Concrete Grinding
For proper adhesion of the epoxy, it is essential that the surface of the concrete is roughened to create an optimal bonding surface. One of the most effective methods to achieve this is through grinding, which not only removes any existing coatings—such as old paint, sealants, or adhesives—but also opens up the pores of the concrete, ensuring the epoxy can deeply penetrate and bond more securely. This process is critical because any remaining coatings or contaminants can prevent the epoxy from adhering properly, leading to premature failures like peeling or bubbling.
In places like residential garages or commercial spaces in St. George, Utah, where previous coatings may have been applied, grinding becomes even more important. These existing coatings must be completely removed to provide a clean, textured surface for the new epoxy layer. The specific environmental factors in St. George, such as temperature fluctuations and dry air, can exacerbate the wear on older coatings, making their removal essential for the long-term durability of the new epoxy floor. By thoroughly grinding the surface, you ensure that the epoxy will not only bond effectively but also withstand the unique demands of the region's climate and usage patterns, providing a durable, long-lasting floor for years to come.
3. Moisture Testing
One of the most overlooked steps in surface preparation is moisture testing. Excess moisture trapped within the concrete can cause serious problems once the epoxy is applied. In St. George, where dry air is the norm but sudden humidity spikes can occur, moisture testing is critical to avoid potential failures.
Moisture testing typically involves using a moisture meter to ensure the surface is dry enough for epoxy application. If moisture levels are too high, a moisture barrier may need to be applied before the epoxy coating.
4. Crack and Imperfection Repair
Cracks, pits, and other imperfections in the concrete surface need to be addressed before applying the epoxy. Any cracks left unrepaired will eventually show through the epoxy floor, compromising its appearance and structural integrity. For both residential and commercial projects, filling these imperfections ensures a smooth, seamless finish.
Crack Filling: Using a high-quality concrete filler ensures that cracks are filled and won’t expand over time.
Surface Patching: If the concrete has significant damage or spalling, larger areas might need patching before proceeding.
5. Priming the Surface
Priming is the final step before applying the epoxy. A primer enhances the bond between the epoxy and the concrete, reducing the risk of bubbles or blisters forming. It also seals the surface, preventing any moisture from rising up into the epoxy layer. For homes and businesses in St. George, using a high-quality primer tailored to the local environment helps ensure that the epoxy floor will stand the test of time.
Common Surface Preparation Mistakes to Avoid
Despite the importance of surface preparation, mistakes can still happen. At Ayala’s Concrete Designs, we’ve seen how errors in this stage can lead to costly repairs and premature floor failure. To avoid these issues, here are common mistakes to watch out for:
Inadequate Cleaning: Skipping a deep clean can leave behind oils, grease, or dust that prevent the epoxy from bonding properly.
Rushing the Process: Surface preparation requires time and precision. Rushing through grinding or crack repair can result in poor adhesion and reduce the floor’s durability.
Skipping Moisture Testing: Ignoring moisture levels can cause bubbling or delamination, especially in climates like St. George’s, where humidity can fluctuate.
Neglecting Crack Repair: Failing to fill cracks or pits leads to weak spots in the epoxy, which can crack over time.
How St. George’s Climate Impacts Epoxy Floor Installation
St. George’s climate presents unique challenges for epoxy floor installations. Understanding these conditions is crucial for long-lasting results. The area is known for its dry, desert-like climate, but sudden humidity or rain can cause moisture to rise from the concrete. Here's how the climate can affect installation:
Heat and Expansion: High temperatures cause concrete to expand and contract, creating cracks that can affect the epoxy layer.
Moisture Retention: Moisture trapped in concrete can lead to blisters in the epoxy, making proper moisture testing critical in St. George’s variable conditions.
At Ayala’s Concrete Designs, we know how to navigate these challenges to provide long-lasting results.

Why Choose Ayala’s Concrete Designs?
Imagine investing in a beautiful epoxy floor, only to see it crack or peel within months due to poor preparation. At Ayala’s Concrete Designs, we believe that a long-lasting, durable epoxy floor starts with meticulous surface preparation. We take the time to clean, test, and repair every surface, ensuring the epoxy bonds perfectly to the concrete.
With years of experience in St. George, Utah, we understand the local climate and conditions. Our expert team tailors each project to meet the unique needs of your home or business, ensuring that your epoxy floor not only looks flawless but is built to last.
By choosing Ayala’s Concrete Designs, you're choosing a partner dedicated to delivering excellence from the ground up. Ready to get started? Contact us today and let us make your next flooring project a success!
Email: [email protected]
Phone: 435-229-7314