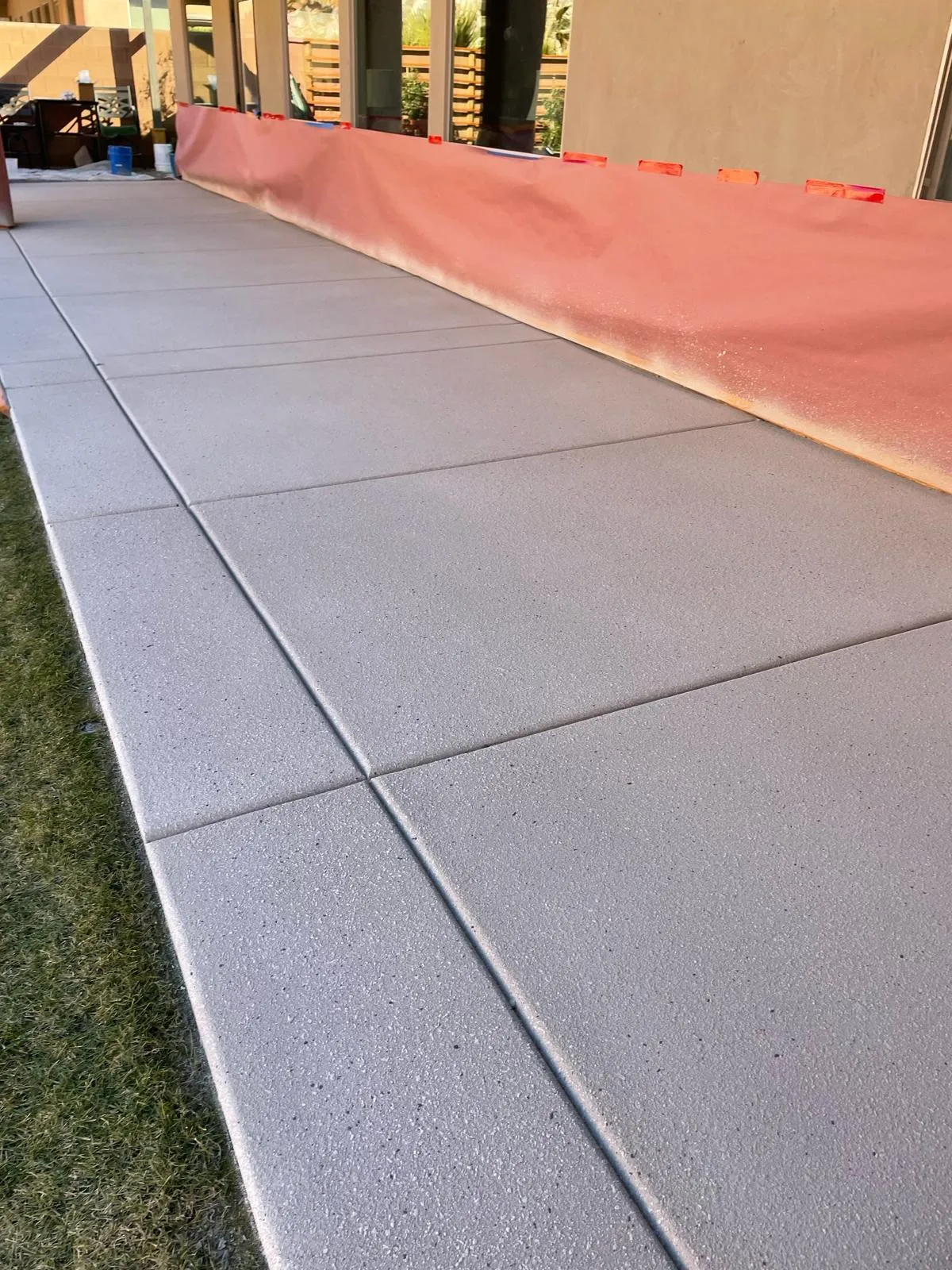
Why Epoxy Coatings Fail: A Comprehensive Analysis for Epoxy Flooring in St. George, UT Client: Ayala’s Concrete Designs in St. George, UT
Epoxy coatings provide a sleek, durable, and chemical-resistant floor covering. Yet, failures do happen when variables such as moisture, substrate preparation, or environmental factors are improperly managed. In St. George, UT, the interplay between temperature, dryness, and potential substrate shifting can be unique. This article explores the most common failure points of epoxy flooring and describes how Ayala’s Concrete Designs meticulously addresses them to deliver high-performance floors to homeowners, businesses, and industrial facilities in the St. George area.
Table of Contents
Introduction
Epoxy Flooring Basics: A Brief Overview
Common Failure Mechanisms
Insufficient Surface Prep
Incompatible Products or Additives
Moisture Vapor Emission
Mixing and Application Errors
Improper Curing and Temperature Extremes
Structural Movements
Chemical and Traffic Loads
Case Studies and Scientific Research
Consequences of Epoxy Failures
Best Practices for Avoiding Failures in St. George
Mitigation Approaches by Ayala’s Concrete Designs
Conclusion
1. Introduction
“If one single step is rushed, an entire epoxy floor can fail.” That cautionary statement rings especially true in the world of flooring. Epoxy is often marketed as an indestructible solution, yet real-life outcomes vary significantly. Some installations last a decade without flinching. Others peel or bubble within months.
St. George, Utah, sits in a desert climate, which means low humidity but fluctuating temperatures. Concrete slabs can shrink and expand in such an environment. Sweeping sand, occasional flash floods, and intense sun all factor into local building conditions. Epoxy floors in St. George face their own distinct hazards, from scorching heat to dryness-driven substrate cracks.
In this comprehensive analysis, we’ll examine why epoxy coatings fail, covering everything from product chemistry to mechanical loads. We’ll also highlight how Ayala’s Concrete Designs implements rigorous, research-based protocols to ensure each floor remains intact over the long haul. Our goal is to provide a clear, authoritative perspective and give you the knowledge necessary to make an informed decision about epoxy flooring for your property.
2. Epoxy Flooring Basics: A Brief Overview
Epoxy coatings are formed by mixing a resin (often a polyepoxide) with a hardener (polyamine or other curing agent). Once combined, a chemical reaction begins. That reaction results in a hardened, cross-linked polymer that adheres to a properly prepared surface. Epoxy is valued for its strength, glossy finish, and resistance to solvents, chemicals, and abrasion.
In commercial and industrial settings, epoxy floors can handle forklift traffic, machine loads, and chemical spills. In residential applications, they transform drab garages into showrooms. However, epoxy is neither flexible nor tolerant of sloppy workmanship. It demands attention to detail.
When installed correctly, epoxy forms a bond that can outlast many other flooring types. But poor substrate prep, moisture intrusion, or incorrect curing conditions can undermine it. This article delves into each of those pitfalls through a scientific lens.
3. Common Failure Mechanisms
3.1 Insufficient Surface Prep
Concrete is full of pores, dust, and micro-cracks. Epoxy relies on a mechanical bond to these pores for maximum adhesion. If the floor isn’t cleaned or roughened properly—through grinding or shot blasting—the epoxy can’t latch on. Later, you’ll see flaking or delamination. Sanding or etching alone may not always suffice, especially if the surface was previously sealed or coated. Removing contaminants is paramount.
3.2 Incompatible Products or Additives
Not all epoxies are created equal. Some have fast cure times, some are more flexible, some incorporate decorative flakes or metallic additives. When mixing different brands or adding pigments unsuited for that specific resin-hardener blend, chemical compatibility issues arise. These can manifest as incomplete curing or compromised strength. The safest route is to follow the manufacturer’s guidelines precisely.
3.3 Moisture Vapor Emission
St. George may be dry, but moisture can still move upward from below the slab. If your concrete lacks a proper vapor barrier or if groundwater creeps underneath, the resulting vapor pressure can push against the epoxy. That pressure forms blisters or bubbles. High vapor drive is a silent killer of epoxy floors in many regions. While desert climates usually have less ambient humidity, moisture can still lurk below ground.
3.4 Mixing and Application Errors
Epoxy requires precise ratios and thorough mixing. Adding more hardener doesn’t make it cure faster in a stable way. It makes it cure incorrectly. Insufficient mixing leaves pockets of resin or hardener that never fully react. During application, uniform thickness matters. Overly thick layers can trap solvents or cause exothermic heat buildup. Thin layers can fail to achieve the necessary structural integrity.
3.5 Improper Curing and Temperature Extremes
In St. George, summer days can exceed 100°F. Epoxy cures faster under higher temperatures, which can create issues with leveling or outgassing. In winter, temperatures may drop sharply at night, slowing the cure or causing dew to form. Both extremes risk incomplete bonding. Maintaining a controlled environment and stable substrate temperature is essential.
3.6 Structural Movements
Concrete expands and contracts. Cracks form from shifting soils, seismic activity, or normal settlement. Epoxy is rigid. It does not stretch much. If the substrate moves, the epoxy can tear or fracture along those lines. Proper crack repair and joint treatment mitigate this risk, but ignoring cracks often leads to floor failures.
3.7 Chemical and Traffic Loads
Factories, warehouses, and even some commercial kitchens expose floors to heavy vehicle traffic. Over time, epoxy can wear down if it lacks the right thickness or topcoat. Chemical spills, especially acids, can eat away at certain epoxies that aren’t rated for chemical environments. Repeated exposure to cleaning solvents can cause micro-degradation. Without the correct formula or protective topcoat, these stressors undermine the floor’s integrity.
4. Case Studies and Scientific Research
Scholarly journals document numerous epoxy failures tied to insufficient moisture mitigation. One paper described a scenario where 80% of installed floors developed blisters within 12 months due to high vapor emissions from the underlying slab. Another study found that mixing errors accounted for 25% of commercial epoxy floor defects, highlighting how small mistakes in ratio measurement can have colossal effects.
Local anecdotal evidence abounds. Ayala’s Concrete Designs has encountered floors where the previous contractor used a single pass with acid etch as the only prep. Within weeks, the coating peeled. Our team had to strip everything and start over with mechanical grinding. The difference was night and day once the surface was properly prepped.
5. Consequences of Epoxy Failures
Epoxy floor failures aren’t just eyesores. They carry tangible costs.
Operational Downtime: For businesses, torn-up floors can halt production. Repairs often involve intense labor, requiring you to close off the area.
Reputation Damage: Customers judge your facility by its appearance. A peeling, bubbled floor undermines confidence.
Safety Hazards: Chips or delaminated sections pose tripping risks. In high-traffic environments, that’s unacceptable.
Additional Expenses: Fixing a failed floor isn’t cheap. It can easily exceed the initial installation cost if large areas need removal and reapplication.
Waste of Resources: Epoxy materials aren’t inexpensive. Failed jobs mean wasted product and time.
6. Best Practices for Avoiding Failures in St. George
St. George’s climate adds specific challenges. High heat can cause rapid cure, while occasional flash floods can raise moisture levels unexpectedly. To combat these:
Test, Don’t Guess: Conduct moisture tests like Calcium Chloride or in-slab probes. Inspect for existing cracks. Evaluate substrate dryness thoroughly.
Mechanical Prep: Ensure diamond grinding or shot blasting to create the right surface profile. Etching alone might suffice in rare cases, but usually mechanical profiling is best.
Temperature and Humidity Control: Time the installation to avoid extreme temperatures. If needed, use fans or climate control solutions.
Correct Product Selection: Ayala’s Concrete Designs recommends high-temperature-tolerant epoxy blends for St. George’s scorching summers. For chemical-heavy areas, we suggest specialized chemical-resistant topcoats.
Joint Treatment: Fill expansion joints with flexible materials. Repair cracks properly with epoxy injection or polymer-modified fillers before the topcoat.
Professional Mixing: Use calibrated containers or weigh the components for precision. Scrape the sides and bottom of the bucket. Mix at the recommended speed and duration.
Cautious Application: Apply each coat as specified. Don’t rush. Don’t overroll. Watch for bubbles and outgassing.
7. Mitigation Approaches by Ayala’s Concrete Designs
We’ve spent years refining our approach to epoxy flooring in St. George. Our success hinges on meticulous process control.
Initial Assessment
A seasoned technician visits the site, measuring moisture with professional-grade tools. They examine cracks, substrate integrity, and gather info on how the floor will be used. A high-traffic auto shop needs different considerations than a residential garage.
Prep Work
We usually employ diamond grinders to profile the surface. This ensures a uniform texture that promotes adhesion. Our vacuum systems control dust, preventing particulate contamination. If the existing floor is heavily soiled or sealed, we take extra steps like repeated passes with increasingly coarse grinding pads.
Moisture Barriers
For slabs that show elevated moisture, we install moisture barrier epoxies or use specialized primers designed to block vapor. We never proceed with standard epoxy if the substrate moisture is too high. That’s a recipe for disaster.
Precise Mixing
Our technicians weigh each component to ensure consistent ratios. We use mechanical mixers, scraping every inch of the container. We also track pot life (the window before the mixture starts to set) to avoid partial cures. Using fresh mixing materials for each new batch prevents cross-contamination.
Climate Control
In mid-summer heat, we schedule installations early in the morning or after sundown. We can deploy fans or portable HVAC to keep the environment stable. We pay attention to substrate temperature as well, not just ambient air temperature.
Crack and Joint Management
We treat cracks with high-strength fillers and flexible sealants if there’s ongoing movement. This step matters more in St. George’s environment, where the ground can shift due to dryness and occasional heavy rainfall. Proper sealing prevents micro-cracks from telegraphing through the new coating.
System Customization
Ayala’s Concrete Designs offers multiple epoxy types. For garages, we might suggest a polyaspartic topcoat for UV stability. For industrial clients, we might use 100% solids epoxy with added thickness. By tailoring the product to the client’s usage needs, we reduce the risk of stress-related failures.
Final Inspection and Maintenance Guidance
We walk the client through best practices—like avoiding harsh chemicals or repeated impact on a brand-new floor. We highlight how to clean up spills and schedule periodic inspections. Maintenance prolongs the life of any epoxy system.
8. Conclusion
Epoxy floors carry a reputation for strength, but that strength hinges on methodical preparation and climate-aware installation. Failures arise from neglected details: overlooked moisture, sloppy mixing, or ignoring substrate movement. These lapses can transform an otherwise durable floor into a peeling, cracking liability.
In St. George, UT, weather extremes demand special care. Temperatures can soar, dryness can cause slab shifts, and unexpected downpours can spike humidity. A proven epoxy system accounts for these variations. That system includes moisture testing, mechanical prep, correct product selection, and precise execution.
At Ayala’s Concrete Designs, we blend scientific rigor with hands-on expertise. Our mission is to deliver epoxy floors that withstand local conditions and daily wear for years to come. When each step is taken seriously, epoxy rarely fails. Instead, it lives up to its promise of longevity, chemical resistance, and polished appeal.
If you’re interested in an epoxy floor that holds up to St. George’s weather and your daily demands, contact us:
Ayala’s Concrete Designs
Phone: 435-229-7314
Email: [email protected]
We’ll assess your site, recommend a tailored system, and ensure no step is overlooked. Don’t let a subpar job lead to headaches down the line. Get it done right from the start.